Retour aux actualites 19 janvier 2021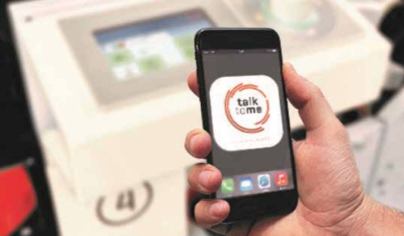
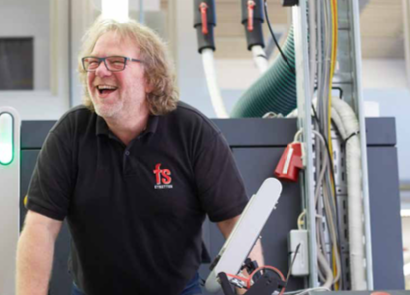
Laissez le workflow
La technologie et la connectivité continuent de se développer rapidement, leurs taux de mise en œuvre augmentant dans toutes les entreprises modernes. De même, dans l’industrie de l’impression, l’intégration et l’automatisation des processus en ligne et hors ligne deviennent une réalité. Déroulements et rembobinages automatisés, processus d’inspection, opérations de finition du rembobinage de la tourelle au refendage, vernissage et dorure à froid. Cette tendance s’étend aux développeurs de systèmes d’information de gestion (SIG), aux éditeurs de logiciels et aux fabricants d’équipements qui collaborent pour mettre en œuvre des améliorations de production significatives.
L’automatisation des flux de travail intègre de plus en plus tous les processus et étapes de production, qu’il s’agisse des informations de gestion, du prépresse, de la presse et d’autres étapes du processus. C’est sans aucun doute la direction que prend l’industrie en ce qui concerne la gestion des presses à imprimer et des usines de transformation de demain.
«Les imprimantes ne fonctionnent pas en moyenne 30% du temps. Ce temps d’arrêt peut être facilement transformé en une capacité de production supplémentaire et transformé en profit supplémentaire »
Laisse la machine parler
«La combinaison de ces technologies permettra de découvrir le potentiel caché des machines et peut apporter jusqu’à 30% d’amélioration des performances», déclare Atze Bosma, PDG de MPS Systems. «Il existe un monde d’opportunités dans l’industrie de l’imprimerie en matière de connectivité et de service basé sur les données. Nous souhaitons montrer à nos clients comment améliorer les performances de leurs presses. » La plate-forme de connectivité de MPS «Talk to me» permet à ses presses de communiquer avec les logiciels et le matériel sur le sol de l’imprimerie, permettant un échange de données multidirectionnel.
En conséquence, les opérateurs et la direction de la presse peuvent obtenir un contrôle total du processus d’impression et prendre des décisions instantanées basées sur les données pour chaque étape. «Nous croyons fermement qu’il existe un réel potentiel d’augmentation de l’efficacité d’une machine à imprimer, mais ce n’est pas réalisable sans une collecte et une analyse correctes des données», ajoute Bert van den Brink, directeur technique de MPS.
«La connexion de notre presse d’imprimerie, du système MIS de Cerm et de la prépresse d’Esko nous donne un ensemble clair de données, ce qui nous aide à identifier exactement où se produisent les inefficacités et comment y remédier pour augmenter la productivité globale.»
«Les trois systèmes individuels offrent un ensemble intéressant de fonctionnalités qui peuvent facilement améliorer la productivité des convertisseurs», commente Geert Van Damme, directeur général de Cerm. «Mais l’interaction entre ces systèmes offre une dimension supplémentaire qui peut être comparée à n’importe quel sport d’équipe: c’est la façon dont ils jouent ensemble qui les fait gagner.» Selon Tim Klappe, directeur général de MPS Asia Pacific, le plus grand gain d’une analyse approfondie est de permettre aux imprimeurs de surveiller les détails des performances et d’utiliser ces connaissances pour identifier les goulots d’étranglement et les points faibles de leurs lignes de production afin de réagir en conséquence.
«Le coût des presses à étiquettes varie entre 300 000 et 3 millions d’euros. Ce sont des équipements sophistiqués. Cependant, les informations que nous pouvons normalement extraire de ces machines sont très limitées. Nous pouvons surveiller la vitesse, les erreurs mécaniques ou électriques et parfois les informations de pression ainsi que les données d’enregistrement », explique Klappe. «Il n’existe pas d’option pour savoir comment fonctionne exactement la machine. Nous ne savons pas combien de temps il faut pour le configurer, quel est le gaspillage de matière exact, le temps de disponibilité, les temps d’arrêt ou même la vitesse moyenne d’une machine par jour ou par semaine. «
Bien sûr, nous pouvons compter sur les opérateurs de machines pour saisir manuellement certaines de ces données, mais ce ne seront pas des informations en temps réel et ne seront certainement pas aussi précieuses ou précises que les centaines de mesures par minute que la technologie des capteurs moderne peut fournir. ‘
Double digitale
En utilisant plusieurs centaines de capteurs attachés à une machine, MPS a créé un modèle jumeau numérique pour permettre la lecture des données. «Avec un flux de données détaillé et continu, nous pouvons comprendre exactement ce qui se passe avec la presse à un moment donné en détail. Pas seulement les 10 à 20 scans que les opérateurs peuvent effectuer manuellement pendant l’exécution du travail; avoir un jumeau numérique avec des ensembles de données dynamiques en streaming permet une meilleure prise de décision », ajoute Klappe.
Le flux constant de données en temps réel ouvre de nouvelles opportunités analytiques sous la forme d’un tableau de bord en ligne facilement accessible. Les convertisseurs d’étiquettes n’ont plus à attendre les rapports de productivité car toutes les informations importantes sur leurs lignes de production sont rassemblées sur le tableau de bord virtuel. Selon Klappe, ces analyses en continu rendent les propriétaires d’entreprise plus agiles et plus réactifs aux réalités de ce qui se passe dans l’opération d’impression d’étiquettes. «La majorité des convertisseurs d’étiquettes se remémorent les performances passées», note-t-il. «Aujourd’hui, les données de production en temps réel peuvent être comparées aux informations historiques pour donner à la direction une perspective immédiate sur le développement de l’entreprise. L’analyse en continu permet à la direction d’être proactive avec un traitement et une prise de décision en temps réel au lieu d’être simplement réactive aux données plus anciennes. Les convertisseurs ont la possibilité d’être plus rapides que leurs concurrents et de gagner en capacité supplémentaire grâce à la mise en œuvre continue des meilleures pratiques, à la réduction des erreurs et des temps d’arrêt.
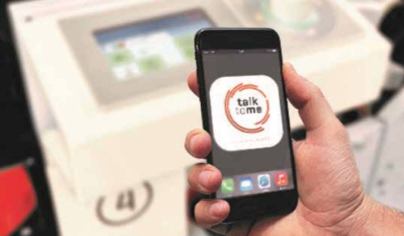
«Nous pourrions parler de plusieurs secondes de gain, une minute ici et une minute là-bas dans un temps de configuration plus rapide. Cela peut ne pas sembler particulièrement excitant au début. Cependant, ces gains de temps peuvent facilement se traduire par des heures par semaine et des semaines par an. Selon nos recherches, les machines à imprimer ne fonctionnent pas en moyenne 30% du temps. Ces temps d’arrêt peuvent être facilement transformés en une capacité de production supplémentaire et en bénéfices supplémentaires pour les transformateurs. » «Vous pouvez comparer l’échange de données en temps réel entre les systèmes (matériel et logiciel) et le SIG avec l’entrée d’un panneau de commutation dans une gare», ajoute Geert Van Damme. «Lorsqu’un train a passé un aiguillage (changement d’état en prépresse, par exemple plaques prêtes), le train suivant peut commencer à circuler (l’impression est possible). Le MIS est le panneau de commutation, vérifiant toutes les conditions pour le workflow complet.
Le matériel, le logiciel et l’opérateur signalent les changements d’état (signaux de commutation) qui remplissent des conditions consécutives ou parallèles pour les étapes suivantes. Si cet échange de données en temps réel n’existait pas, les opérateurs devraient activer / désactiver manuellement ou informer l’opérateur suivant qu’il est prêt à partir (comme ils l’ont fait il y a des années en mettant le ticket de travail sur la boîte de réception -pile de l’opérateur suivant en ligne).
Maintenant, ils voient tous les instructions sur leur écran pour la prochaine tâche en ligne lorsque les conditions sont définies automatiquement. »
Parler de la machine
Cerm et Esko ont estimé qu’en intégrant simplement le SIG et le logiciel de prépresse, les convertisseurs sont déjà en mesure d’augmenter considérablement leurs performances de production. L’efficacité renforcée par une seule entrée de données réduit le gaspillage et les erreurs jusqu’à 80% et en automatisant les processus, le temps de traitement peut être réduit jusqu’à 50%.
Le flux constant de données en temps réel ouvre de nouvelles opportunités analytiques sous la forme d’un tableau de bord en ligne facilement accessible. Les convertisseurs d’étiquettes n’ont plus à attendre les rapports de productivité car toutes les informations importantes sur leurs lignes de production sont rassemblées sur le tableau de bord virtuel. Selon Klappe, ces analyses en continu rendent les propriétaires d’entreprise plus agiles et plus réactifs aux réalités de ce qui se passe dans l’opération d’impression d’étiquettes. «La majorité des convertisseurs d’étiquettes se remémorent les performances passées», note-t-il. «Aujourd’hui, les données de production en temps réel peuvent être comparées aux informations historiques pour donner à la direction une perspective immédiate sur le développement de l’entreprise.
Ces gains offrent aux transformateurs la possibilité de traiter plus de 40% de travaux en plus en utilisant le même nombre de presses à imprimer et d’opérateurs. La cartographie de la chaîne de valeur (VSM) d’Esko se concentre sur le flux de travail de création de valeur d’une entreprise, exposant les gaspillages et les retards en fonction des chiffres réels et des informations recueillies auprès des employés, et révélant les opportunités d’améliorer la productivité et le débit. VSM considère le workflow comme un système d’étapes et d’activités qui sont toutes liées d’une manière ou d’une autre, aidant les dirigeants à établir une stratégie zéro déchet à long terme plutôt que d’entreprendre des actions singulières.
C’est le point de départ d’un projet d’amélioration des affaires. Ken Polspoel, responsable des solutions globales chez Esko, commente: «VSM vous oblige à penser de manière holistique. Il ne sert à rien de créer des îlots de succès dans une mer de déchets. » «
Le système met à jour les conditions dans les horaires de travail, ce qui conduit à des décisions telles que le report des travaux lorsque les conditions ne sont pas remplies et le replanification des travaux prêts pour la production à une position plus précoce et plus optimale (par exemple en utilisant le même papier / matrice / couleurs) qui conduit – à son tour – à un coût de production moins élevé (moins de temps de changement et moins de gaspillage de matière) », ajoute Geert Van Damme.
«Si vous pouvez toujours être plus efficace que prévu, cela peut entraîner une baisse des prix de vente avec la même marge pour battre la concurrence.»
«Avec un flux de données détaillé et continu, nous pouvons comprendre exactement ce qui se passe avec la presse en détail à un moment donné» Outre l’efficacité de la machine, permettre aux systèmes de communiquer introduit les convertisseurs d’étiquettes à la cohérence et à la qualité des données utilisées dans les différents départements et réduit considérablement le besoin de communication entre le département de pré-presse, les clients et les services clients, ce qui permet des économies de temps et de coûts considérables.
«Nous parlons à nos partenaires, tels que les fournisseurs UV, les fournisseurs de rouleaux anilox, les fabricants de systèmes d’encrage pour les inviter à se connecter avec nous également», déclare Klappe. «Nous pouvons connecter tous les éléments de la production d’étiquettes et nous prenons actuellement des décisions sur les appareils à relier à notre réseau de collecte de données. Je suis certain d’un fait; ce développement ne s’arrêtera pas. Au contraire, il accélérera encore plus vite. »
«Cela ne finira jamais», dit Geert van Damme. «Il existe de nombreuses machines qui ne peuvent pas encore être connectées et celles qui atteignent un premier niveau peuvent toujours faire mieux. Même avec Esko, depuis environ 17 ans, nous continuons à travailler ensemble sur de nouveaux flux de travail, basés sur l’expérience et les demandes de nos clients. Cela conduit, par exemple, à une mise en œuvre plus rapide de nos systèmes, à l’intégration entre nos systèmes ou à l’automatisation des flux de travail pour les nouveaux produits de notre industrie. »
Théorie en pratique
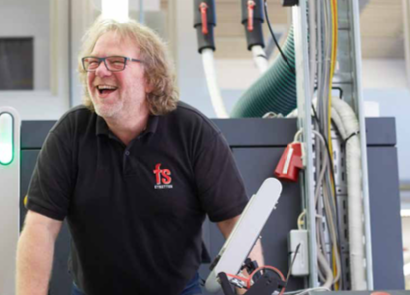
«Pour moi, MPS est le premier constructeur de presse en termes de technologie», déclare Bernd Koch, directeur de l’information chez fs-Etiketten, un convertisseur d’étiquettes familial basé à Friesenheim, dans le sud de l’Allemagne. «MPS est toujours à la pointe des innovations et est le leader dans le domaine de la connectivité. La connectivité est quelque chose qui m’intéressait déjà et MPS m’a donné l’opportunité d’en faire l’expérience de première main en effectuant un essai dans notre usine de production. »
La plate-forme de connectivité «Talk to Me» associée à la nouvelle machine était essentielle pour Koch. « Les avantages de cette plate-forme sont qu’elle est plus rapide, le temps de changement est plus court, il y a moins de gaspillage et la connectivité nous demande moins, car tout est contrôlé de manière centralisée par le SIG avec lequel nous travaillions déjà », dit-il.
«Grâce à la connectivité multidirectionnelle, nous pouvons organiser et contrôler nous-mêmes l’ensemble du processus de production. Cela nous fait gagner beaucoup de temps. »
Koch a une vision claire de la fonctionnalité du système «Talk to me» et des avantages qu’elle présente pour son entreprise. «La plate-forme de connectivité fonctionne de manière entièrement automatique. S’il y a un travail d’impression sur la machine, nous utilisons la fonction de mémoire des travaux pour prendre les préréglages de la presse », explique-t-il.
«Lorsque l’opérateur va configurer le prochain travail d’impression sur le terminal, la presse est déjà automatiquement installée dans la bonne position, par conséquent, le changement est très rapide. Comme le temps de passage est celui où vous ne gagnez pas d’argent, vous voulez le garder aussi court que possible. Grâce à la plate-forme de connectivité, il y a plus de temps pour la production d’étiquettes entièrement converties. Plus l’automatisation est élevée, plus la productivité est élevée. » fs-Etiketten travaille avec l’échange de données MIS de la plate-forme de connectivité. «Toutes mes attentes sont satisfaites», poursuit Koch. «Maintenant, les améliorations instrumentales doivent avoir lieu; nous voulons intégrer encore plus les systèmes. En ce moment, nous travaillons avec quatre terminaux sur la machine, chacun avec une tâche différente. Un écran est pour la caméra d’inspection AVT, un pour le contrôle du registre CC1, un pour le Cerm MIS et un pour la caméra optique BST. Nous aimerions voir tous les systèmes connectés afin que nous puissions connaître une augmentation encore plus grande de la productivité. »
Pour fs-Etiketten, «Talk to Me» a prouvé ses avantages dans la production quotidienne car l’entreprise parvient à minimiser les déchets, à accélérer les temps de changement et à augmenter la productivité. «Comme nous étions le premier client MPS à disposer de la plateforme« Talk to Me »en phase de développement, nous avons pu collaborer avec MPS. Nous pensons que cette façon de travailler est la voie à suivre. Nous avons constaté les avantages presque immédiatement après la mise en œuvre de la plate-forme. Grâce à la connectivité multidirectionnelle, nous pouvons organiser et contrôler nous-mêmes l’ensemble du processus de production.
Cela nous fait gagner un temps considérable. Pour l’instant, l’essai ne signifie pas d’investissement en capital, mais nous investirions certainement car je peux voir les immenses avantages qu’il offre », conclut Koch.
L’avenir est ici
Toutes les nouvelles presses MPS, expédiées depuis le début de cette année, sont déjà équipées d’un serveur de périphérie permettant la collecte multidirectionnelle des données. Il peut également être installé sur la majorité des presses EF produites jusqu’en 2018. «Cela ne signifie pas que des améliorations continues se produisent simplement en installant ce type de technologie», prévient Klappe. «Non, la technologie nous donne des informations.
Connaissance des lignes de production et du fonctionnement. Nous pouvons en rendre compte et présenter plusieurs suggestions sur ce que nous pensons qu’il devrait se passer pour améliorer l’opération. Cependant, c’est le convertisseur d’étiquettes qui doit être ouvert à recevoir des connaissances et surtout ouvert à prendre des mesures pour améliorer l’efficacité de la production. Les entreprises qui réussissent intégreront ces analyses en continu pour passer d’une approche réactive à une approche plus proactive de l’excellence opérationnelle.